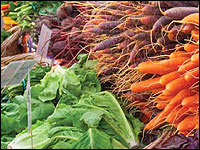
Part 1 of this series explores the practical aspects of locating greenhouses in urban environments.
These are not your grandpa’s greenhouses.
Anyone familiar with common plastic-enclosed passive solar structures designed simply to hold plants over cold seasons or grow flowers and less-hardy fruits might be surprised about how these humble buildings have transformed into today’s dynamic hydroponic “bio-structures.”
The modern high-tech greenhouse represents the timely convergence of some of the most sophisticated scientific know-how available from a variety of industries — agriculture, horticulture (the scientific cultivation of fruits, vegetables, herbs, flowers and ornamental plants in nurseries and gardens), energy (solar, wind and fuel cells), greenhouse manufacturing, hydroponics (soil-less growing), environmental control software, lighting, heating and ventilation, polymers and many more.
Properly built and operated, these state-of-the-art, computerized food producing machines can enclose valuable unused urban space in glass to produce abundant crops of commercially grown food for local consumption.
Controlling the Environment
Controlled Environment Agriculture (CEA) is a high-tech industry for the production of food crops, flowers, houseplants and medicinals within controlled environment greenhouse structures.
“Once food production is put on a rooftop — or any confined area — the need to develop intensive, high-productivity, year-round growing systems demands CEA technologies,” said Gene Giacomelli, director of the Controlled Environment Agriculture (CEA) Program at the University of Arizona.
CEA combines engineering, plant science and computer-managed greenhouse control technologies used to optimize plant growing systems, plant quality and production efficiency. CEA systems allow stable control of the plant environment, including temperature, light and CO2 (which plants must absorb in combination with water, nutrients and sunlight to produce the sugars vital for their growth). CEA also provides separate control of plant root-zone environments.
Computer-coordinated CEA activities include environment control (encompassing air temperature and movement, humidity, supplemental light and CO2 concentration) and mechanization and automation of operations that were formerly done by hand-mixing, fertilizing and placing root media, seeding and transplanting, nutrition management, hydroponic crop production, “fertigation” and material movement at harvest.
“Systems from many companies have been developed during the past 30 years to monitor and control greenhouses for flower and vegetable production,” Giacomelli told TechNewsWorld. “They were developed to improve the capabilities of CEA, the quality of the products, the savings of labor allowed by automation, and the effectiveness of sensors that can at times more accurately determine the environment or climate of the crop, and then immediately make necessary changes.”
Green Tech
A “gold standard” already exists for hydroponic greenhouses. The North American Greenhouse/ Hothouse Vegetable Growers (NAGHVG) was founded by leading North American greenhouse growers: Village Farms, Eatontown, N.J.; Windset Farms, Delta, British Columbia; Eurofresh Farms, Willcox, Ariz.; Houweling’s Hot House Nurseries, Camarillo, Calif., and Delta, B.C.; and Gipaanda Greenhouses, Ladner, B.C. Based in Bellingham, Wash., the NAGHVG has developed a “Certified Greenhouse” program. Standards include:
- Every aspect of the growing process is monitored and controlled, from irrigation to climate control and growing medium.
- Vegetables can be protected from pollution, wildlife and other potential contaminants, which creates conditions for the safest possible produce-growing methods.
- Eco-friendly integrated pest management (IPM) is used.
- The greenhouses must be able to provide reliable supplies of produce throughout the year.
The NAGHVG’s “Certified Greenhouse” program involves ongoing audits to ensure that certified producers continue to meet the standards set by the association. Certification is granted exclusively to greenhouse operations that comply with NAGHVG’s definition of a greenhouse:
- Facility includes a fully enclosed permanent aluminum or steel structure clad either in glass or impermeable plastic for the controlled-environment growing of certified greenhouse/hothouse vegetables.
- Facility must use computerized irrigation and climate control systems, including heating and ventilation capabilities.
- Facility must use hydroponic methods and must grow produce in a soilless medium that substitutes for soil.
- Facility must practice IPM.
Greenhouse Hardware/Software
Computers can operate hundreds of devices within a modern greenhouse (vents, heaters, fans, hot water mixing valves, irrigation valves, curtains. lights. etc.) by utilizing dozens of input parameters, such as outside and inside temperatures, humidity, outside wind direction and velocity, CO2 levels and even the time of day or night. A computer can keep track of all relevant information such as temperature, humidity, CO2 and light levels. It dates and time-tags the information and stores it for current or later use. Such a data acquisition system enables a grower to gain a comprehensive understanding of all factors affecting the quality and timeliness of the greenhouse product.
Dozens of software developers have developed CEA-oriented applications. Major players include:
- Priva: automated climate and process control in the horticultural and building intelligence markets;
- Argus Control Systems: automated control systems;
- Hoogendoorn Growth Management: process automation systems;
- Micro Grow Greenhouse Systems: greenhouse environmental control systems;
- Link4 iGrow: intelligent environmental controllers.
Virtual Grower is a decision support tool for greenhouse growers to monitor plant growth and control energy management in greenhouses. It was developed by the U.S. Department of Agriculture (USDA) Agricultural Research Service (ARS) Application Technology Research Unit at the University of Toledo (Ohio). Users of the software can build a virtual greenhouse with a variety of materials for roofs and sidewalls, design the greenhouse style, schedule temperature set points throughout the year, and predict heating costs for over 230 sites within the continental U.S. Different heating and scheduling scenarios can be predicted with the input of a few variables, with accurate data based upon historical records collected by USDA monitoring stations across the country.
“Specific software is not important,” said UA’s Giacomelli. “But including it within a monitoring and control system that is dependable and effective is one of the most important aspects of CEA with emphasis on urban agriculture.”
Solar and wind power are the two primary renewable energy forms most commonly used by greenhouses for energy sources that are “off-grid” — not connected to an electricity distribution system. A third technology is fuel cells.
Solar Energy
Active solar greenhouses use supplemental energy to move solar-heated air or water from storage or collection areas to other regions of the greenhouse.
PVs are arrays of cells containing a solar photovoltaic material that converts solar radiation into direct current electricity. Materials presently used for photovoltaics include silicon, cadmium telluride and copper indium selenide/sulfide.
Building-integrated photovoltaics (BIPVs) are increasingly incorporated into new domestic and industrial buildings as a principal or ancillary source of electrical power, and are among the fastest growing segments of the PV industry. Typically, an array is incorporated into a building’s roof or walls, and roof tiles with integrated PV cells can now be purchased. Arrays can also be retrofitted into existing buildings.
Productivity is also improving. Since flat solar panels only get direct sunlight for three to four hours per day, Sunflower Solutions developed a patent-pending manually adjusted solar power tracking system that dramatically increases the amount of sunlight that solar arrays can capture.
In addition to free-standing PV solar arrays, greenhouses can capture solar energy through the use of enclosures made of a special PV glass with integrated solar cells that convert sunlight into electricity. The solar cells are embedded between two glass panes and a special resin is filled between the panes, securely wrapping the solar cells on all sides. Each individual cell has two electrical connections, which are linked to other cells in the module to form a system which generates a direct electrical current. This means that the power for a greenhouse can be produced within the roof and facade areas. Manufacturers include SCHOTT and Pythagoras Solar.
The growing demand for renewable energy sources has dramatically advanced the manufacture of solar cells and photovoltaic arrays in recent years. However, due to expenses related to implementation, use of solar electric (photovoltaic or PV) heating systems for greenhouses remains cost-prohibitive for most small businesses unless used to produce high-value crops.
Wind Power
Wind turbines are mechanical rotary devices that extract wind energy and convert it to electricity. In addition to traditional turbines utilizing familiar paddle-shaped blades, a new class of vertical-axis helical turbines from companies like San Diego-based Helix Wind have proven to be superior in producing electricity in the variable winds of urban environments. Using the twisted-ribbon shape of a helix, these generators overcome problems like noise, impact and price. Helical turbines are nearly noiseless because they spin at the same speed as the wind blowing into them.
Small “hybrid” electric systems that combine wind and solar technologies offer several advantages over either single system. Many hybrid systems are standalone units operated off-grid. For times when neither the wind nor the solar systems are producing, most hybrid systems provide power through batteries and/or an engine generator powered by conventional fuels, such as diesel. If the batteries run low, the engine generator can provide power and recharge the batteries.
Adding an engine generator makes the system more complex, but modern electronic controllers can operate these systems automatically. An engine generator can also reduce the size of other components needed for the system. The storage capacity must be large enough to supply electrical needs during non-charging periods.
Fuel Cells
Since traditional renewable energy technologies like solar and wind are often intermittent, greenhouse operators have turned to fuel cells as an energy alternative. Fuel cells convert air and nearly any fuel source like hydrogen, natural gas or a wide range of biogases into electricity via a clean electrochemical process, rather than dirty combustion. Even running on a fossil fuel, the systems are much cleaner than a typical coal-fired power plant.
Fuel cells are devices that produce a continuous electric current directly from the oxidation of a fuel, e.g., that of hydrogen by oxygen. They were invented over a century ago and have been used in practically every NASA mission since the 1960s. But until now, they have not gained widespread adoption because of their inherently high costs.
Legacy fuel cell technologies like proton exchange membranes (PEMs), phosphoric acid fuel cells (PAFCs), and molten carbonate fuel cells (MCFCs) have all required the use of expensive precious metals, corrosive acids or hard-to-contain molten materials. Combined with performance that has been only marginally better than alternatives, they have not been able to deliver a strong enough economic value proposition to overcome resistance.
Among the newest technologies is the solid-oxide fuel-cell (SOFC), available from companies like Bloom Energy and Technology Management. The technology is gaining wide acceptance due to its use of low-cost ceramic materials and its extremely high electrical efficiencies. In addition to their use as auxiliary power units in vehicles, SOFCs can be used for stationary power generation in greenhouses, with outputs from 100 W to 2 MW.
Developed originally by SOHIO/British Petroleum, the TMI system operates on a range of liquid and gas fuels and is designed for operation and maintenance by end-users without special tools, equipment or access to a trained service workforce.
SOFC is an ideal alternative energy technology of choice for greenhouse applications, according to Tim Madden, president of Akron, Ohio-based hydroponic greenhouse development firm Biodynamicz, which is integrating TMI’s fuel cells into its designs.
“We’re focused on SOFCs as auxiliary power sources because they’re able to convert a wide variety of fuels like hydrogen, methane, butane or even gasoline and diesel, and because they do it with such high efficiency,” Madden told TechNewsWorld. “TMI’s SOFCs are attractive as energy sources because they’re clean, reliable and almost entirely nonpolluting. And because there are no moving parts, the cells are vibration-free and quiet, which eliminates the noise pollution associated with power generation.”
Fuel cell technology improvements are continuing to come from places like the automotive industry and so prices will continue to drop as production quantities increase.
Let There Be Light
As for the use of modern light-emitting diode (LED) semiconductor technology in plant grow lights, LEDs present many advantages over traditional lighting technologies like high pressure sodium (HPS) and High Intensity Discharge (HID).
When electric current flows through an LED, electrons travel through an energy “bandgap” in the diode crystal, releasing energy in the form of light. This effect is called electroluminescence and the color of the light is determined by the materials used to make the LED. A single LED grow light directly replaces 600-watt HPS light while consuming 50 percent less energy and is rated for a lifecycle of 50,000 hours. Cool-running LED lights also eliminate the need for ballasts (current regulators in lamps), reflectors, noisy fans or expensive cooling systems.
Even though LED technology is more expensive than traditional HID lighting, the units require less maintenance, bulb replacement costs are eliminated, savings on energy costs start from day one of ownership, and total ROI is generally 12 to 18 months.
A recent IMS Research report stated that while Nichia, Osram Sylvania and Philips Lumileds remain the leading suppliers of packaged LEDs, they are being challenged by companies in Taiwan and Korea, notably Seoul Semiconductor.
Leading manufacturers of LED grow lights for greenhouses include LumiGrow and Lighting America of Ohio.
“Artificial lighting is too expensive to install and operate to be economical in vegetable production due to the high amount of natural sunlight needed, especially for crops like strawberries and tomatoes,” Verti-Gro’s Tim Carpenter told TechNewsWorld. “LED light does not offer a full spectrum of light for flowering vegetables and fruits. LED for commercial use is a ways off but is improving rapidly, especially for vertical growing. I believe there will still be a need for a substantial amount of real sunlight in order to produce vegetables and berries profitably.”
BioDynamicz’ Madden likes LED lighting in greenhouses.
“The light produced from an LED source is better absorbed by plants, and greenhouse growers have been trying for years to eliminate hot HID fixtures because heat can damage crops,” he explained. “LEDs solve that problem.”