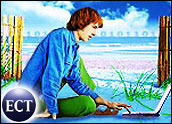
Part 1 of this series looks into the issue of PC recycling and following the course of a hypothetical laptop through the recycling process. Continuing down this path, this part will consider another situation: Laptop owner Joe Verdi doesn’t own a laptop from a brand name OEM with a take-back program.
He wants to recycle it and he gets lucky, or is clued-in about the shady global trade in e-waste, and he finds an honest, ethical PC recycler in his area that’s going to do the job right. The laptop will likely follow a similar path if it’s turned into any of the take-back, recycling programs run by major laptop manufacturers.
The laptop will likely be reconditioned and sold second-hand or broken down for parts rather than recycled. That’s the main reason costs to recyclers and prices to laptop owners turning their machines in at recycling centers are lower than they otherwise would be.
“There still is a fair amount of residual value in laptops — they are in higher demand. We charge about US$2.50 to process a laptop — a little below the market average, but we get so many,” explained Jeremy Farber, president of PC Recycler.
“Only 20 percent are actually recycled; the rest get reconditioned and reused,” he added. “We work with a couple of companies that reuse the parts, even plastic casing,” he added.
Down the Recycling Stream
If it’s recycled in the U.S. rather than reused or exported overseas for dismantling and dumping, Joe’s laptop will wind up at an independent recycling ship or in an OEM’s (original equipment manufacturer) in-house recycling program.
With centers in Virginia and New York, PC Recycler is one of a many recyclers whose business is increasing as consumers become more environmentally conscious and investments in new businesses and recycling value chains gain market traction. Though the company, which is privately held, doesn’t disclose revenues, Farber said PC Recycler’s business grew 160 percent by weight of PCs processed year over year.
The OEMs exert a big influence on the profitability of independent recyclers, according to Farber.
For one thing, large OEMs’ in-house recycling programs compete with independent recyclers. In addition, each manufacturer has its own particular design, parts and assembly specifications, which add to the difficulty and cost of recycling laptops to independent recyclers.
“You can’t process a laptop mechanically; you have to manually remove a few components,” Farber elaborated.
For instance, laptops’ circuit boards and plastic casings are treated with potentially toxic brominated flame retardants. Transformers and capacitors contain PCBs (polychlorinated biphenyls), and monitors and other devices are chock full of a host of heavy metals, including lead, zinc, cadmium and chromium. Their lighting contains mercury, which qualifies as a hazardous material. Similarly, batteries have to be treated as hazardous waste.
“These have to be removed and shredded, and that’s complicated,” Farber said. “You can’t just start shredding laptops; those mercury lights have to come out.”
“The manufacturers don’t make it easy — they use nonstandard configurations. They’re manufactured different ways by different manufacturers; the assembly is completely different, so that forces us to have a higher standard worker and process to recycle them,” Farber continued.
Recovering Rare and Precious Metals
Precious, rare earth and base metals — such as indium, lithium, bismuth, ruthenium, platinum, nickel and gold — are essential to producing PCs, and prices for them have been rising dramatically in recent years. Their higher prices, along with advances in recapturing them from e-waste and the development of a supporting recycling industry value chain, is making recycling more economically feasible. Attracting sufficiently high volumes is the key to market success, however.
The price of indium — a compound that is used in making flat screens and more than a billion products per year — has increased six-fold in the last five years, making it more expensive than silver.
While known mine reserves are limited, indium recycling has been taking place in a few plants in Belgium, Japan and the U.S. Japan recovers roughly half its indium needs through recycling, according to the United Nations University (UNU), home of the UN Solving the E-Waste Problem (StEP) initiative’s secretariat.
“The large price spikes for all these special elements that rely on production of metals like zinc, copper, lead or platinum underline that supply security at affordable prices cannot be guaranteed indefinitely unless efficient recycling loops are established to recover them from old products,” UNU professor Ruediger Kuehr stated.